X-Ray Chair - master of design thesis
Mid-century designers leveraged post-WWII manufacturing techniques to blend form and function. This thesis demonstrated the similar capability of a designer with an engineering skillset. Following the examples set by past mid-century modern designers, a chair design project in injection molding was performed and discussed.
​
The research concludes that engineering methodologies alone in product design are often too limited in defining constraints, and that some professionals should operate in the same space in which all products live—between engineering and design. Conducting a design project inside of this “space between” resulted in an authentic product (one whose aesthetic direction is driven by constraints) as well as other key advantages.
Island Lamp - product design studio
Teamed up with Clay Brown (ID) and Sarah Schonauer (CODE), we designed a lamp inspired by historic Cincinnati traffic lights. We iterated several prototypes until landing on our final version, and made fifteen of them to sell at a pop up shop in Over the Rhine, Cincinnati.
​
The wire loop at the top of the shade is twisted to turn the lamp on/off and dim the light.
​
The lamp is mostly made of resin components which were cast in silicone molds. A lighting studio helped us source switches and cables. Other parts were machined by the Rapid Prototyping Center at DAAP.
Feed Shoe - component redesign
During my time at Kyocera-Senco, I specialized in plastic injection molding. I designed various plastic components, including one called the 'feed shoe.' I updated the old design for the new tool. After the engineering was done, the part looked just like the previous one, which I felt was a missed opportunity. Since the new design required updated tooling anyway, the aesthetic could be changed at no extra cost. My dual role as an engineering-designer came into play, reworking the component to be more ergonomic and contemporary. The department approved my design direction, and these changes were implemented into mass production.
​
This project ignited my passion for industrial design, leading me to become an engineering-designer and pursue a Master of Design degree.
Sculpture Foundry - a foray in fine art
I follow the notion that the field of "making things" is a spectrum. If engineering is on one side and fine art on the other, then design lies along the middle. To push out of my typical engineering wheelhouse, I wanted to explore the processes of fine art.
Working in a foundry with sculptors expanded my knowledgebase and gave me more insight into different mantras of making. Plus, this very manufacturing-adjacent process reinforced my materials knowledge in practice.
​
We used lost-wax investment casting to produce bronze and aluminum sculptures.
Conceptual Airplanes - form/function
Growing up near CVG airport, I was always fascinated with airplanes. I feel as though they are humankind's peak designed object. When learning rapid ideation through sketching and modeling, the form of an aircraft was a familiar and beloved subject to experiment with.
​
Most of my concepts are fantastical, but always rooted in some idea or feature based in reality. I strive to maintain a deep connection between form and function as my brand of design.
DAAP Grant Project - firefighter safety
​As a Master of Design student at UC, I worked on a grant project focusing on enhancing the safety and effectiveness of firefighter suits. This experience let me practice in the space between design and engineering.​
My role centered around being a liaison between engineering and design, including industrial and mechanical design, data analysis, sewing industrial samples, working with advanced materials, and developing composites. The team achieved DAAP's highest-ever grant funding for two years, and I worked on this project for my entire DAAP career.​
I am listed as the primary inventor of the cooling apparatus on UC's patent application draft.
Crystal Cabin - patented by Boeing
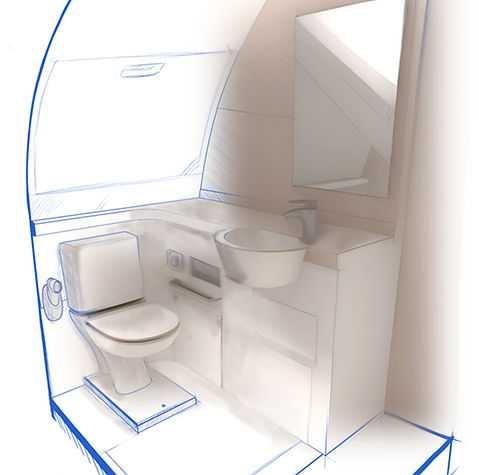
In a collaboration with Live Well design studios and Boeing, I made several cabin concepts based on thorough design research. One of my concepts, an adaptable lavatory system, was selected to become Boeing intellectual property and submitted to the international award competition for cabin design - the Crystal Cabin Award 2024, where the concept was shortlisted.
Additional development of the concept for the Crystal Cabin Award was done collaboratively-- thanks to Henry Levesque for modeling support and Fiat Tongrod for rendering.